Ladle refractory materials are key materials used in the steelmaking process to protect the ladle lining and withstand the erosion of high-temperature molten steel and slag. As the main container for holding and transporting molten steel (from converter/electric furnace to continuous casting tundish), the refractory materials of the ladle need to remain stable under extreme thermodynamic and chemical conditions, while adapting to frequent molten steel impact, temperature changes and violent reactions at the slag-steel interface. The following are the key components, performance requirements and technical challenges of ladle refractory materials:
What are ladle refractory materials?
Ladle refractory materials are mainly composed of ladle lining and ladle refractory functional products. Its internal refractory materials need to withstand extreme conditions such as scouring, chemical erosion and thermal shock of high-temperature molten steel.
Ladle lining is usually divided into the following parts according to different areas in contact with molten steel and functional requirements:
Permanent layer (safety layer):
Material: lightweight insulation bricks or low thermal conductivity castables (such as clay).
Function: thermal insulation, reducing the temperature of the ladle shell and reducing heat loss.
Working layer (direct contact with molten steel and slag):
Slag line area:
Material: magnesia carbon brick (MgO-C, containing 10%~20% graphite).
Features: High resistance to slag erosion (especially against alkaline slag), graphite provides thermal shock resistance and lubricity.
Wall area:
Material: aluminum magnesium carbon brick (Al₂O₃-MgO-C) or high aluminum castable (Al₂O₃≥80%).
Features: Balances resistance to molten steel erosion and cost, suitable for non-slag line areas.
Bottom area:
Material: high aluminum brick or corundum castable (Al₂O₃≥90%).
Features: High mechanical strength, resistance to molten steel static pressure and impact wear.
Functional components:
Refractory sliding gate:
Material: aluminum zirconium carbon composite (Al₂O₃-ZrO₂-C) or magnesium carbon (MgO-C).
Function: Accurately control the flow of molten steel, and need to resist high temperature erosion and thermal shock.
Purging plug:
Material: corundum-spinel (Al₂O₃-MgAl₂O₄) or magnesium (MgO).
Function: Stir the molten steel by blowing argon/nitrogen, uniform temperature and composition, high permeability and anti-permeability are required.
Well Block:
Material: high aluminum or magnesium carbon.
Function: Fix the gate and withstand the mechanical impact of molten steel flow.
Performance requirements of ladle refractory materials
- Slag erosion resistance: The slag line area of the ladle needs to resist the chemical erosion of high-basicity slag (CaO/SiO₂>2).
- Thermal shock resistance: The temperature fluctuates greatly during the ladle turnover (such as cooling an empty ladle from 1600°C to room temperature), and the material needs to avoid cracking.
- High temperature strength: Withstand the static pressure of molten steel (such as the bottom pressure of a 200-ton ladle reaches ~0.3MPa) and mechanical shock.
- Low pollution: Avoid impurities in refractory materials (such as SiO₂) from reacting with molten steel and affecting the purity of steel.
Evolution and challenges of material technology
Optimization of magnesia carbon bricks
Traditional magnesia carbon bricks: Rely on graphite to improve thermal shock resistance, but graphite is easily oxidized (antioxidants such as Al and Si need to be added).
Low carbonization trend: Develop low-carbon magnesia carbon bricks (graphite content <8%), replace part of the graphite with nanocarbon (such as carbon black) or in-situ generated carbon structure (such as resin carbonization) to reduce oxidation risk.
Environmental protection and chromium-free
Chromium pollution problem: Traditional magnesia-chrome bricks (MgO-Cr₂O₃) are restricted due to the carcinogenicity of Cr⁶⁺.
Alternative solution: Use spinel (MgAl₂O₄) or magnesium-calcium (MgO-CaO) materials, which are both slag-resistant and environmentally friendly.
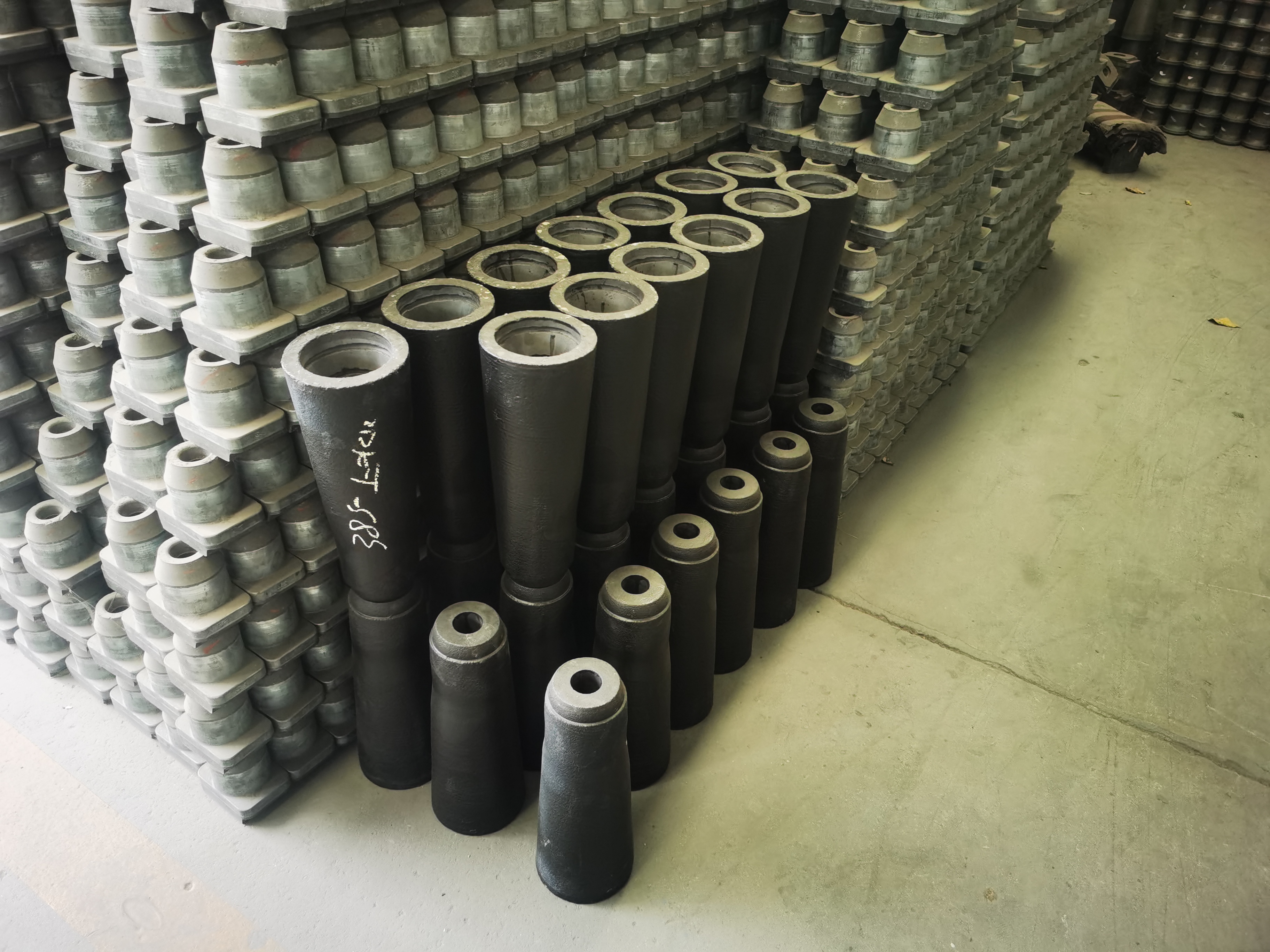
Extension of castable application
Integral casting technology: Use alumina-magnesia or spinel castables to replace traditional brickwork, reduce joint erosion and extend service life.
Self-leveling castables: Vibration-free construction is achieved through particle size optimization, reducing labor costs.
Typical failure modes of ladle refractory materials
Slag line erosion: Slag penetration causes the formation of low-melting-point phases (such as CaO-MgO-SiO₂ system) on the surface of magnesia-carbon bricks, and the structure peels off.
Thermal stress spalling: Frequent temperature changes cause the expansion of microcracks inside the material, and eventually the layered shedding.
Blockage of air bricks: inclusions in molten steel (such as Al₂O₃) are deposited in the air holes, affecting the argon blowing effect.
Application of ladle refractory materials:
Clean steel smelting: Use high-purity corundum air bricks (Al₂O₃>99%) to reduce the introduction of impurities.
Long-life design: Optimize cost and life through gradient structure (such as magnesium carbon bricks in the slag line area and aluminum-magnesium castables for the ladle wall).
Intelligent monitoring: Use infrared thermal imagers or acoustic emission technology to monitor the erosion status of the ladle lining in real time.
Ladle refractory materials are the core consumables in the steelmaking process, and their performance directly affects the quality of molten steel, production safety and cost. Compared with tundish refractory materials, ladle materials need to withstand longer molten steel residence time, more complex slag-steel reactions and higher mechanical loads. Future development directions include low-carbon and environmentally friendly materials, long-life design and intelligent maintenance technology. For example, the application of magnesium-calcium materials and carbon-free castables can not only improve slag resistance but also meet the requirements of green manufacturing.