The name of the refractory nozzle comes from its function - the word "nozzle" vividly describes its role as a melt channel, while "refractory" highlights its durability in high temperature environments. According to its specific use, refractory nozzles can be divided into many types, such as upper nozzles, lower nozzles, collector nozzles, submerged entry nozzles (SEN), etc. Each type has differences in structure and materials to meet different process requirements.
What is a refractory nozzle?
Refractory nozzle is a refractory material product used for high-temperature molten metal (such as molten steel, molten iron) or non-metallic melt flow control, usually installed in the outlet or sliding nozzle system of metallurgical equipment (such as ladle, converter, tundish).
It ensures the stability and safety of the smelting and casting process by accurately controlling the flow rate, flow rate and flow direction of the melt. Refractory nozzles not only need to withstand extreme high temperatures (usually over 1500°C), but also must resist chemical erosion, mechanical scouring, and thermal shock damage from melt and slag.
Composition and materials of refractory nozzles
The performance of refractory nozzles depends directly on their material selection and structural design. The following are its main components and material characteristics:
1. Main materials
Aluminum carbon (Al₂O₃-C): High-purity alumina (Al₂O₃) is used as the main component, and carbon materials (such as graphite) are added to enhance thermal shock resistance and erosion resistance. Aluminum carbon nozzles are widely used in ladles and tundishes, and are suitable for casting ordinary carbon steel.
Aluminum zirconium carbon (Al₂O₃-ZrO₂-C): Zirconium oxide (ZrO₂) is added to aluminum carbon to improve resistance to high temperature erosion and thermal shock, and is suitable for high manganese steel or other special steel grades.
High-alumina: With high-alumina bauxite as the main raw material, it is suitable for low-requirement occasions or ordinary carbon steel casting, and has a low cost.
Magnesium-carbon (MgO-C): With magnesium oxide (MgO) as the matrix, carbon materials are added, suitable for high-alkalinity slag environment or special steel grades.
Fused quartz: Used for casting some low-carbon steel or non-ferrous alloys, it has good thermal shock resistance, but weak erosion resistance.
Composite materials: such as composite nozzles with zirconium oxide core and high-aluminum outer layer, combining the advantages of different materials to optimize performance.
2. Structural design
Refractory nozzles are usually cylindrical or conical, with precise flow channels inside (aperture is generally 10-100 mm) to control the melt flow rate. Some nozzles (such as immersion nozzles) are designed with special shapes, such as side holes or elliptical outlets, to optimize the flow field distribution of molten steel in the crystallizer. The outer layer may be covered with a metal sleeve (such as an iron sleeve) to enhance mechanical strength and prevent thermal shock cracking.
3. Functional additives
To improve performance, the following additives are often added to refractory nozzles:
Antioxidants: such as silicon (Si) and aluminum (Al) powders, to prevent carbon materials from oxidizing at high temperatures.
Stabilizers: such as oxides such as calcium (CaO) and magnesium (MgO), to enhance thermal shock resistance and erosion resistance.
Binders: such as resins and asphalt, to improve molding strength and high-temperature stability.
Functions of refractory nozzles
Refractory nozzles perform multiple key functions in high-temperature metallurgical processes:
1. Flow control
Refractory nozzles precisely control the flow rate and flow of the melt through the size and shape of their internal flow channels. For example, in the continuous casting process, the submerged nozzle cooperates with the sliding nozzle system to adjust the speed at which the molten steel enters the crystallizer to avoid defects caused by too fast or too slow.
2. Protect the melt
The submerged nozzle goes deep into the crystallizer to prevent the molten steel from being exposed to the air, reduce oxidation and inclusion formation, and improve the quality of the billet. In addition, the smooth design of the inner wall of the nozzle can reduce turbulence in the melt flow and reduce the risk of slag inclusion.
3. High temperature and erosion resistance
The
refractory nozzle needs to withstand the impact of molten steel or slag at 1500-1700°C. The high refractoriness and erosion resistance of the material ensure that it remains stable during multiple castings and prolongs its service life.
4. Thermal shock stability
When the ladle is replaced or the casting is started and stopped, the nozzle will experience a sharp temperature change. High-quality refractory nozzles reduce the risk of thermal shock cracking by optimizing material formulation and structural design.
5. Prevent clogging
For high-aluminum steel or calcium-containing steel, alumina inclusions may be generated in the molten steel, causing nozzle clogging. Refractory nozzles often use anti-adhesion materials (such as composite materials containing CaO) to prevent clogging by generating low-melting point substances (such as CaO·Al₂O₃).
Application fields of refractory nozzles
Refractory nozzles are widely used in the following fields:
1. Iron and steel metallurgy
Ladle: The upper and lower nozzles are used at the bottom of the ladle, and cooperate with the sliding nozzle system to control the flow of molten steel to the tundish.
Tundish: The collecting nozzle and the immersed nozzle are used to transfer molten steel from the tundish to the crystallizer to optimize the continuous casting process.
Converter and electric furnace: Refractory nozzles are used for the steel outlet to withstand the erosion of high-temperature molten iron and slag.
2. Non-ferrous metal smelting
In the smelting of non-ferrous metals such as aluminum, copper, and magnesium, refractory nozzles are used for melt transmission and casting, such as guide nozzles in aluminum alloy casting.
3. Glass and ceramic industry
Refractory nozzles are used for the flow control of high-temperature glass or ceramic melts, and must have extremely high corrosion resistance and dimensional stability.
4. Other high-temperature industries
Such as garbage incinerators, chemical high-temperature reactors, etc., refractory nozzles are used to control the discharge or transmission of high-temperature fluids.
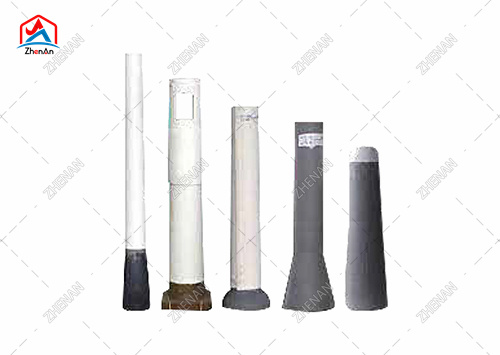
Production process of refractory nozzles
The production of refractory nozzles involves many complex processes to ensure that their performance meets industrial standards:
1. Raw material selection and ingredients
Select high-purity alumina, zirconium oxide, graphite and other raw materials, and strictly control the impurity content. Add antioxidants, binders, etc. according to the formula ratio and mix evenly.
2. Molding
Use isostatic pressing or high-pressure molding technology to ensure that the nozzle structure is dense and the flow channel is precise. Some nozzles (such as immersion nozzles) need to be formed into complex shapes by precision molds.
3. Sintering
Sintering at high temperature (1400-1800°C) in an oxygen-free or protective atmosphere (such as nitrogen) enhances material strength and thermal shock resistance. Some products use secondary sintering or heat treatment to further optimize performance.
4. Surface treatment
Polish the flow channel or apply an anti-adhesion layer (such as ZrO₂ coating) to improve corrosion resistance and fluidity. The outer layer may be covered with a metal sleeve or anti-oxidation treatment.
5. Quality Inspection
The porosity, cracks and dimensional accuracy of the nozzle are checked by non-destructive testing methods such as X-rays and ultrasound. The refractory performance and erosion resistance are verified by laboratory simulation tests.
Advantages of Refractory Nozzles
The wide application of refractory nozzles in high-temperature industries stems from its following advantages:
High durability: high-quality materials and processes ensure that the nozzles can be used for a long time in extreme environments, and the single life can reach several hours to several days.
Precise control: The accuracy of the flow channel design ensures the stability of the melt flow and improves product quality.
Erosion resistance: It has strong resistance to chemical erosion and mechanical erosion of molten steel and slag, reducing maintenance costs.
Thermal shock stability: The optimized material formula reduces the risk of thermal shock cracking and adapts to the process requirements of frequent start-stop.
Diversified design: nozzles of different types and specifications meet various process requirements and have a wide range of application scenarios.
As the core component of high-temperature industry, refractory nozzle integrates multiple functions such as high temperature resistance, corrosion resistance and flow control. It is an indispensable "behind-the-scenes hero" in the iron and steel metallurgy, non-ferrous metal smelting and other industries.